Technical Article
Published 03/2023
The Fundamentals of High Voltage Equipment Grounding
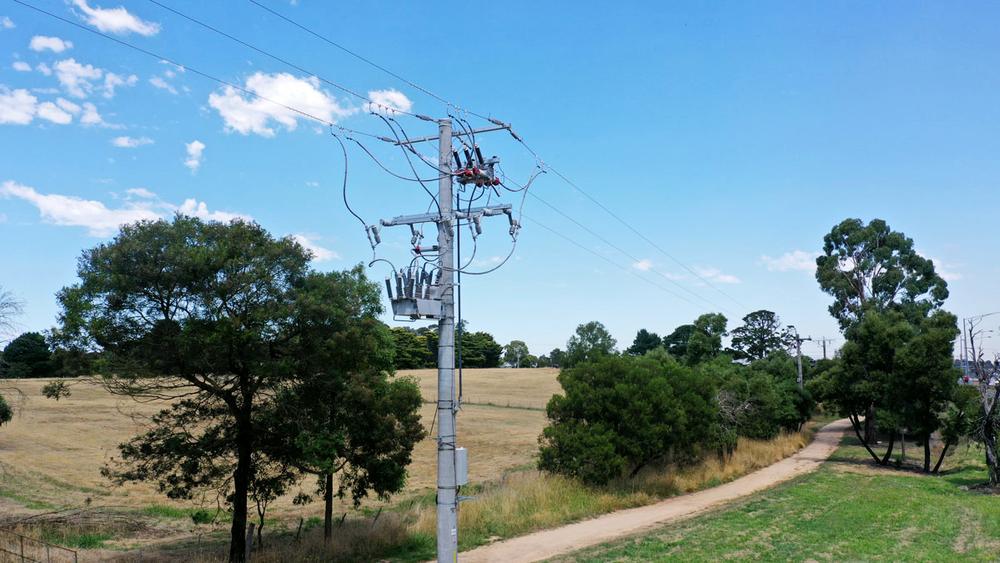
How grounding protects electrical equipment
Grounding protects electrical equipment by providing a safe path for the flow of fault current to the ground. Fault current is the current that flows in the equipment during a fault or short circuit condition. Without grounding, the fault current can flow through the human body or other conductive materials, which can lead to electric shock or damage to the equipment.
When an electrical fault or lightning strike occurs, the fault current flows through the grounding system and into the ground. The grounding system provides a low resistance path for the fault current to flow, which helps to quickly isolate the fault and prevent damage to the equipment.
Grounding also helps to reduce the risk of electrical fires by limiting the build-up of static electricity or other electrical charges. This is because the grounding system allows for the dissipation of these charges into the ground, preventing the accumulation of potentially dangerous levels of electrical energy.
Different methods for grounding electrical equipment
There are several methods for grounding electrical equipment, including:
- Plate Grounding: In this method, a copper or galvanized iron plate is buried in the ground at a depth of about 2 meters. The plate is connected to the equipment through a conductor. This method is suitable for equipment with low voltage and small currents.
- Rod Grounding: In this method, a copper or galvanized iron rod is driven vertically into the ground, and the equipment is connected to it through a conductor. The depth of the rod depends on the soil resistivity and the magnitude of the fault current. This method is suitable for equipment with higher currents.
- Pipe Grounding: In this method, a hollow pipe made of galvanized iron or copper is driven into the ground vertically, and the equipment is connected to it through a conductor. The pipe is filled with coke and salt to increase its conductivity.
- Strip Grounding: In this method, a flat strip of copper or galvanized iron is buried in the ground horizontally, and the equipment is connected to it through a conductor. The strip should be at a depth of about 0.5 meters and should be long enough to provide the required earth resistance.
- Grounding Mat: In this method, a conductive mat made of copper or aluminum is placed below the equipment, and the mat is connected to the earth through a conductor. This method is suitable for equipment with low voltage and small currents.
- Chemical Grounding: In this method, a chemical compound is used to increase the conductivity of the earth. The compound is poured into a borehole, and a copper electrode is inserted into it. The electrode is connected to the equipment through a conductor. This method is suitable for equipment with high fault currents.
It is important to follow the recommended grounding standards and guidelines to ensure safety and proper functioning of the equipment.
Different materials for grounding high voltage equipment
It is important to use materials that can handle the high voltage and current levels without degrading or failing when earthing equipment. Some common materials that can be used for grounding high voltage equipment include:
- Copper: Copper is an excellent conductor of electricity and is widely used for grounding high voltage equipment. It can handle high currents and is resistant to corrosion, making it a durable choice.
- Galvanized steel: Galvanized steel is a good choice for grounding in areas with high soil resistivity. It is also able to handle high currents and is resistant to corrosion. It also has a different frequency response to copper, where the impedance is high for line surges. Therefore, it is not suitable or approved for use with NOJA Power OSM Reclosers.
- Copper-clad steel: Copper-clad steel consists of a core of steel that is coated with a layer of copper. This combination of materials provides the strength of steel with the conductivity of copper, making it a good choice for grounding high voltage equipment.
- Aluminum: Aluminum is a lightweight and inexpensive material that is often used for grounding high voltage equipment. However, it is not as conductive as copper and may require a larger cross-sectional area to handle the same current levels. It also has a different frequency response to copper, where the impedance is high for line surges. Therefore, it is not suitable or approved for use with NOJA Power OSM Reclosers.
- Graphite: Graphite is a relatively new material that is gaining popularity for earthing high voltage equipment. It is highly conductive and can handle high current levels, but is also lightweight and resistant to corrosion.
When selecting materials for grounding high voltage equipment, it is important to consider factors such as conductivity, corrosion resistance, and strength. The appropriate material should be chosen based on the specific requirements of the equipment and the surrounding environment. Additionally, all materials used for grounding must comply with applicable safety standards and regulations.
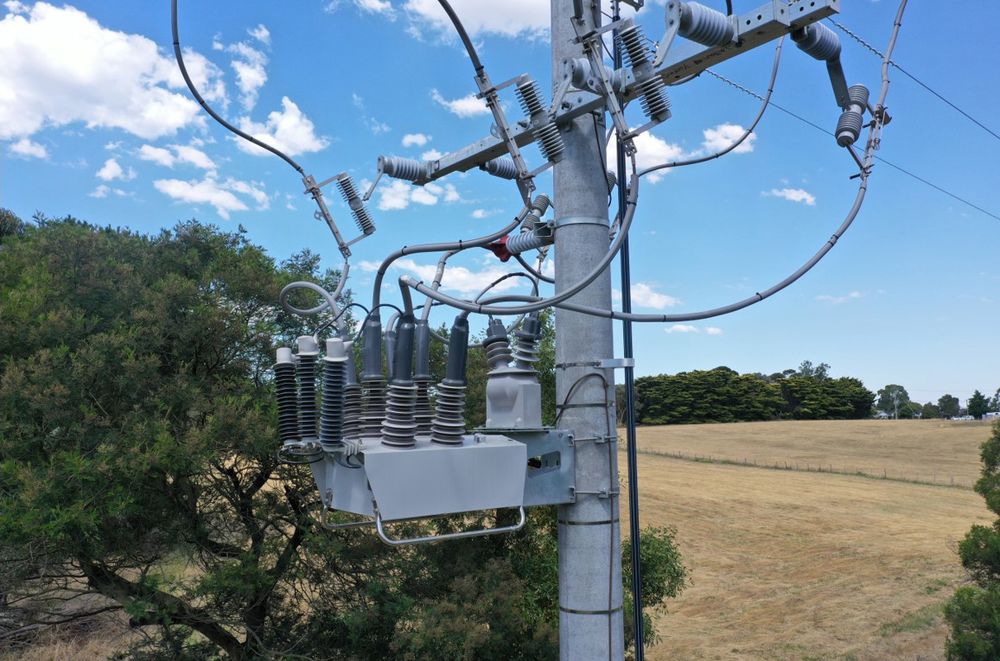
What standards are relevant when choosing grounding materials for high voltage switchgear
There are several standards and guidelines that should be taken into consideration to ensure the safety and reliability of the grounding system. Some relevant standards include:
- IEC 62271-200: This standard covers the design, construction, and testing of high voltage switchgear and controlgear. It provides guidance on the selection of grounding materials and systems, including the requirements for resistance and the use of multiple earthing electrodes.
- IEEE 80: This standard provides guidance on the design and installation of grounding systems for power substations and other high voltage installations. It covers the selection of grounding materials, the design of grounding systems, and the measurement of ground resistance.
- IEC 60364: This standard provides guidance on the design, installation, and maintenance of electrical installations, including grounding systems. It covers the selection of grounding materials, the requirements for resistance, and the use of supplementary electrodes.
- BS 7430: This British standard covers the design, installation, and maintenance of grounding systems for electrical installations. It provides guidance on the selection of grounding materials, the design of grounding systems, and the measurement of ground resistance.
- ANSI/IEEE C2: This American standard provides guidelines for the design and installation of grounding systems for power systems. It covers the selection of grounding materials, the design of grounding systems, and the measurement of ground resistance.
These standards provide guidance on the selection of grounding materials for high voltage switchgear, as well as the design and installation of grounding systems. When selecting grounding materials, it is important to follow these standards and guidelines to ensure the safety and reliability of the earthing system.
What grounding does a NOJA Power OSM Recloser require?
The NOJA Power OSM Recloser requires a suitable grounding system to ensure safe and reliable operation.
“It is critical to earth our equipment correctly in order to achieve a high level of reliability and safety for our products,” says NOJA Power Group Managing Director Neil O’Sullivan.
“It is the most import factor to consider at every installation.”
According to the NOJA Power OSM Recloser manual, a minimum of 35mm2 copper conductor should be used for the OSM Recloser and RC Cubicle. A direct, unbroken link must be made from the OSM Recloser to the earth connection point at the base of the pole. A parallel groove clamp must be used for bonding the RC short length conductor to the unbroken OSM Recloser Earth Conductor.
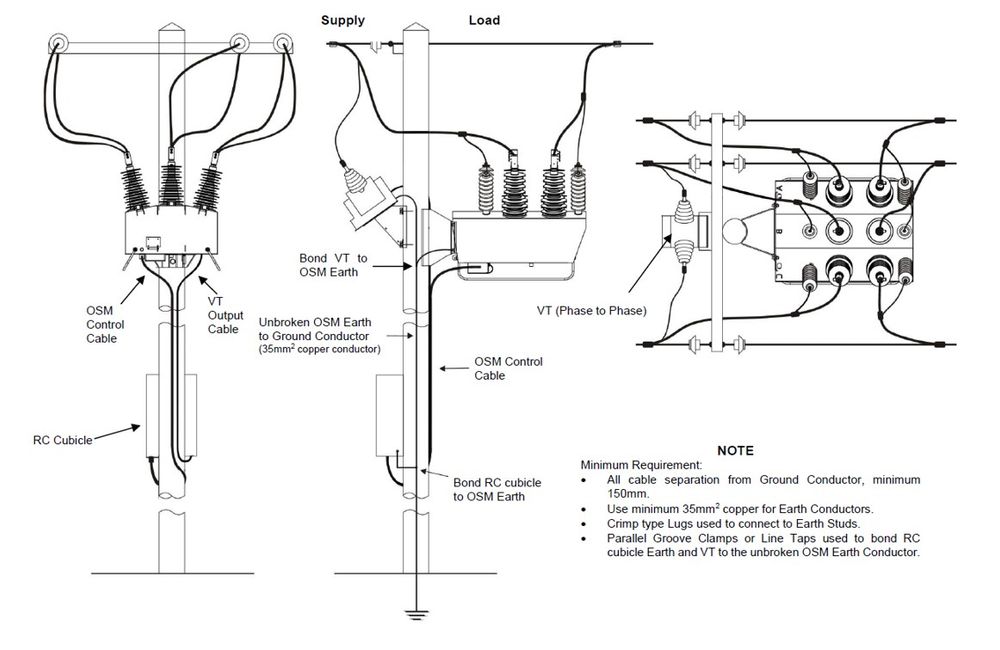
Want to stay up to date with Electrical Distribution Technology?
Join our list for a free weekly technical bulletin, as we share our Global Electrical Engineering experience directly to your inbox.
Subscribe →